
OVERVIEW:
Dewalt is breaking into a new market with a fencing stapler and partnered with our engineer/research team to explore what this tool might look like with human-factors as the driving design criteria.
As designed, the tool was to weigh over 11lbs, with only one grip position, designed for the above 50% male. Having spent many years as a female in the fabrication and carpentry industry I was thrilled for the opportunity to push the boundaries of the usership of a commercial tool, opening up the range of humans who could wield this powerful fencing stapler.
Deliverables included form-factor prototypes and a research deck examining pain points of this tool as designed and the effects of alterations made in the new prototypes to alleviate these pain points.
SKILLS: Design Strategy, Research, Human-factors, Prototype testing
COLLABORATORS: Caitlin Sweet
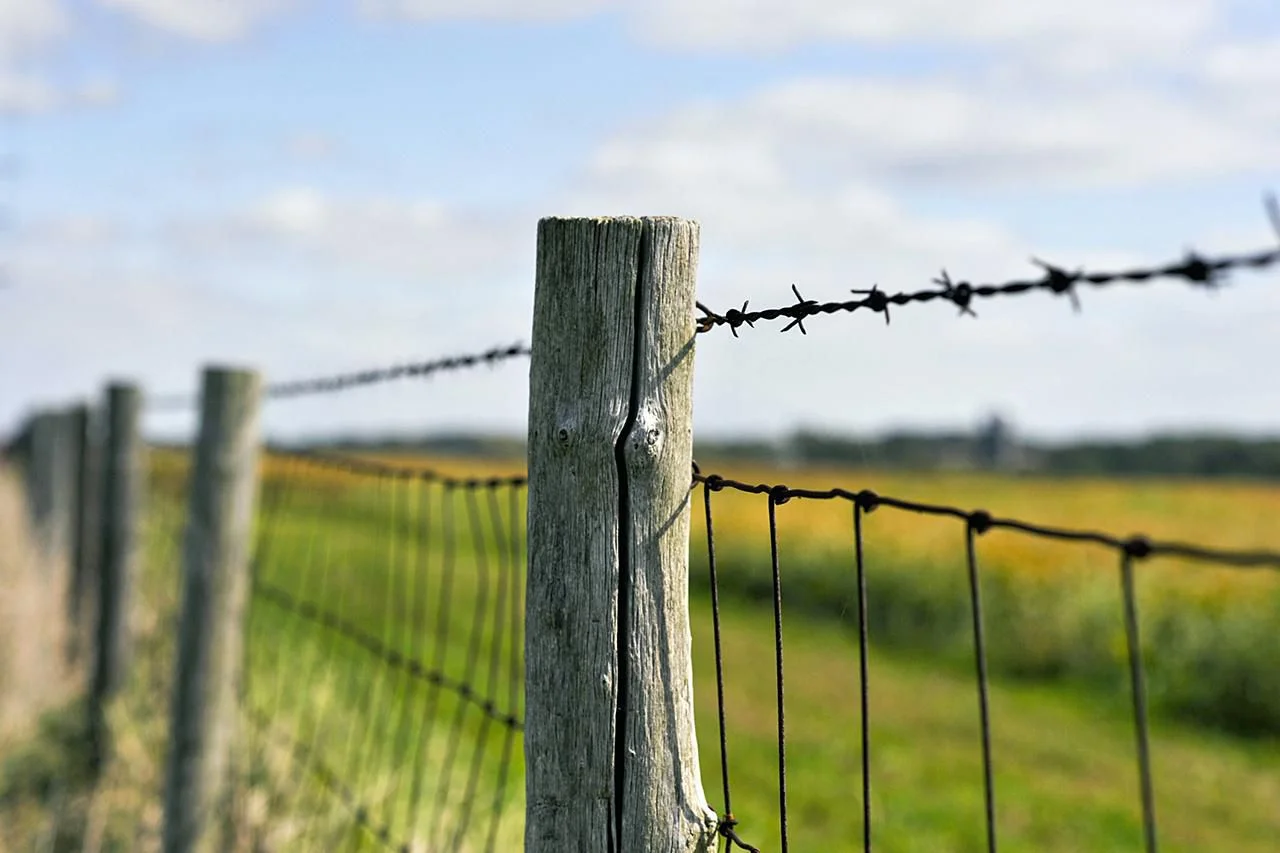
PROCESS
User research relying on observation through video was our first tool in understanding the process of operating a fencing stapler. A visit to Dewalt’s headquarters allowed us to speak with industrial designers and engineers about their current approach on the project. Through research we created a task analysis and identified pain points in the process which guided our re-design.
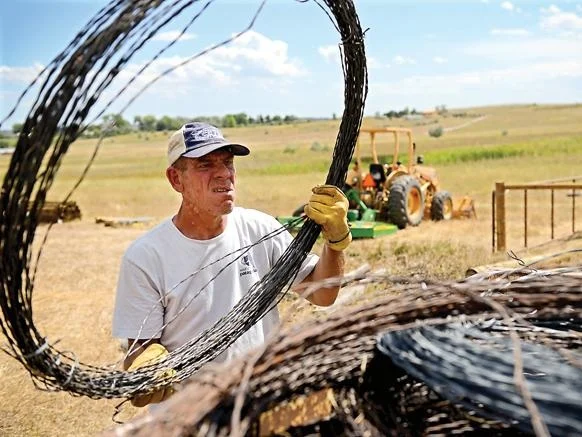
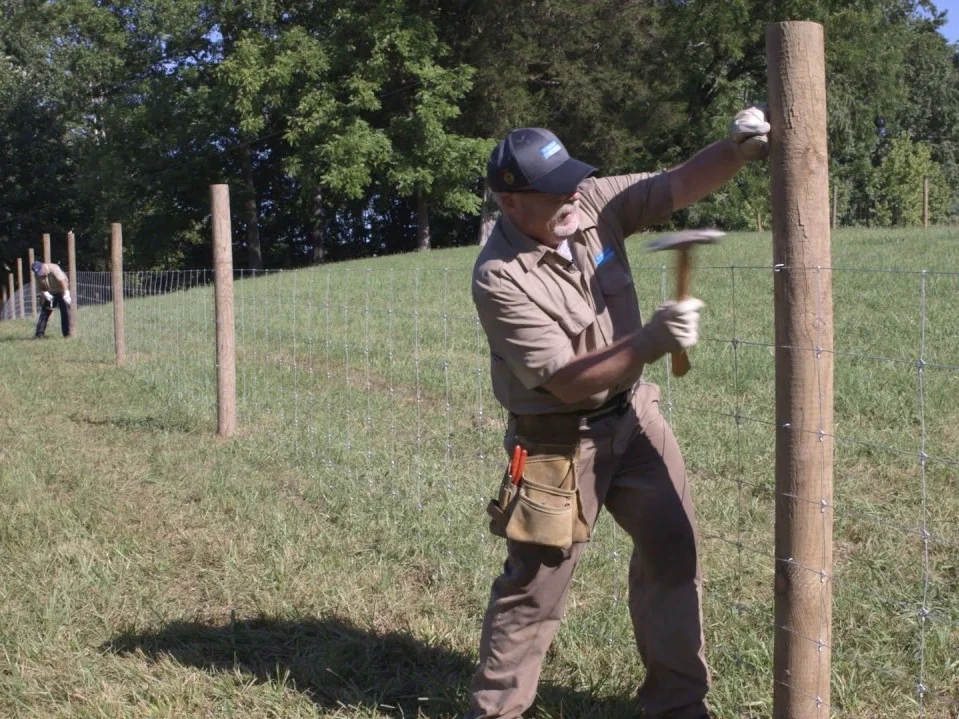
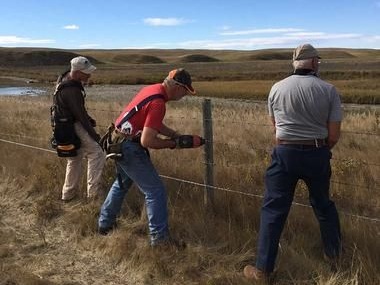



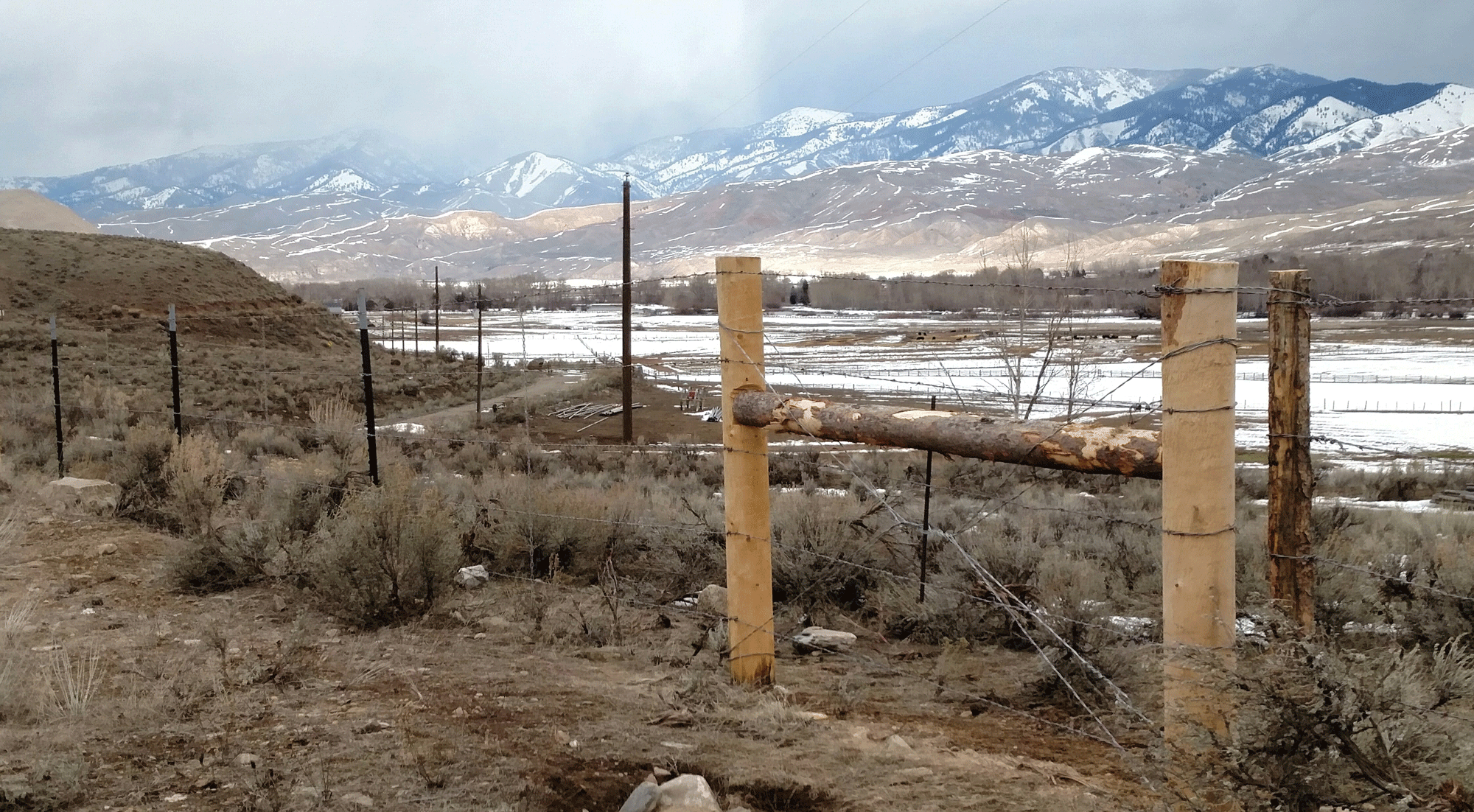
painpoints
Analysis
Task Analysis
Through this systematic breakdown we identify each pain point in the process to examine each as an opportunity for a design solution. Steps violating OSHA’s guidelines are in red
User Needs
Research and this task analysis led us to identify these 7 primary user needs:
These user needs are the design criteria that drove the alterations to the fencing stapler form factor.
SECONDARY RESEARCH: OSHA’s Standards for Power Tools
The Dewalt fencing stapler, as designed, is incongruent with many of OSHA’s recommendations, putting users at risk. We applied OSHA’s standards for power tools in our redesign to avoid injury and create a less strenuous experience for users.
SolutionS
We presented Dewalt with two solutions: a redesign of the physical tool and a tool-balancing rig to offset the weight of the device.
Direction 1:
Redesign of Stapler Components
Working off of Dewalt’s mechanical drawings, we broke the tool into its most basic components and systematically rearranged elements. We landed on two configurations that challenged the concept of the tool as a “gun” and solved pain-points identified in the task analysis. The circular handle rotates around the central barrel to allow the user to insert staples at the angle necessary for the given application. Triggers have been added on the top to eliminate bending.
Stapler with ring or semi-ring handle creates a range of hand hold positions.
Added triggers allow for alterations to grip.
Tool can perch on ground so that user doesn’t have to kneel all the way to the ground.
Tool body will be able to spin and lock, so machine can be set to insert staples at desired angle rather than twisting user’s arm.
Early Prototypes
FEATURES: Redesigned handle= multiple grip options, multiple trigger options, ergonomic hand grips, can stand on handle and end of magazine or lean on handle and motor.
CHANGES FOR NEXT ITERATION: explore potential 45 degree magazine orientation, potential rotation of handle structure
BENEFITS: less strain on same finger, less wrist rotation, less bending because of top handle trigger
WEIGHTED PROTOTYPES


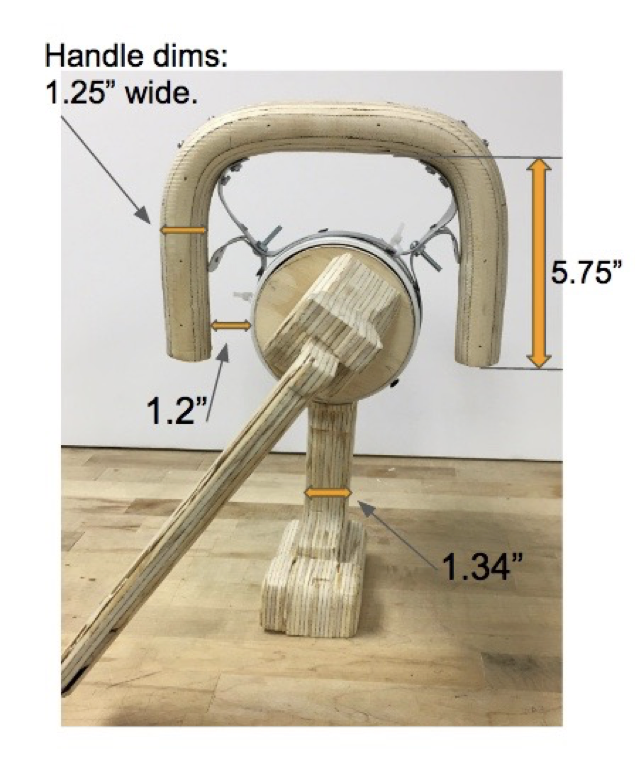

Prototype Testing
We took our prototypes into the “field” for a series of tests against a baseline that we set with an actual Dewalt Nailer. Multiple participants were timed in a series of tasks.
Next we tested the same participants using our rough prototypes that were weighted to match Dewalt’s anticipated tool weight.
The amount of strain and torque was calculated to quantitatively support our redesign.
Eliminating Painpoints
ORIGINAL
Stapler requires pronation/ supination of 45 degrees to insert staple at correct angle.
RE-DESIGN
Magazine is already at 45 degrees, therefore eliminating wrist twisting.
ORIGINAL
Index finger must exert the force to pull the trigger (repetitive, strenuous)
RE-DESIGN
Force is shared between multiple
fingers-reduces repetition and strength required
ORIGINAL
The user has to bend so the head of the tool is 14” above ground, which requires the hand to be apron 11” above the ground.
RE-DESIGN
With top handle, user bends 7” less than with original. Hand is 21” above the ground.
Direction 2:
Tool balancing rig concept
Tool Balancing Rig
Stapler connects to a zero gravity reel that holds the tool where you leave it. You can use both hands and give arms a rest.
Tool can be used by a wider range of users, as it is no longer as strenuous for users’ forearms and wrists.
Rig could be used in many other applications, as well, so makes it a bit more of a convincing purchase for consumers.
Features: counterweight offsets 11lb tool, in combination with a toolbelt, retractable systems to transfer weight to hips and shoulders
Benefits: less strain on arm muscles, reduces potential injury caused by overuse, makes it possible to use tool for longer periods of time. Neutralizing weight allows for a greater range of users.
Prototypes
Mini tool balancer Weighing only .285 lbs, it can counterbalance a tool weighing anywhere between 2 lbs and 12 lbs - perfect for our application.
The wearable rig would transfer the weight from the wearer’s forearm and wrist to the shoulders, hips and back.
Stapler attaches to tool retractor via quick release clip for quick on-off.
Flexible extension arm bends slightly under load. Rig height is adjustable by moving belt loop up or down the extension arm.
Padded shoulder support allows for comfort yet stability. One-strap format allows for great freedom of movement
Secures with adjustable elastic around ribs. Quick-release buckle for easy in/out.
Bottom of extension arm connects to ANY tool belt- through loop on bottom of extension.
Balancing rig prototype testing
Tests were performed against baseline measurements.
The stapler with rig was weighed and the scale detected only 2.9lbs of force.
We tested the rig with multiple users and there was a consensus that at least ⅔ of the weight of the tool was alleviated by the retractor mechanism. Users were surprised by the weight of the tool once they were no longer wearing the balancing rig.
The product would benefit from a higher quality tool retractor. We found that the one-shoulder harness was adequate for the user to keep the extension arm in place.
Testing Results
Weight of the tool felt by the user is 2.9 lbs which makes the maximum torque at the wrist 1.8 lbsf*ft. (original torque is 4.4 lbsf*ft.) This wrist torque is well within OSHA’s recommendations!
Wearing the tool balancing rig results in a 75% reduction in the weight of the tool on the wrist and forearms.
The remaining 8.1lbs is distributed along the shoulder and hips. If the wearer chooses a back-support tool belt this is an easy amount of weight to carry on the hips.
Design can Level the playing field
Through ideation we explored ways of expanding the usership of this stapler to include individuals without as much physical strength as Dewalt’s intended user. We built a strong argument for a product line of tool balancing accessories to accompany heavy tools, which would distribute the weight of the tool to the user’s shoulders and hips. Currently we’re developing prototypes of zero-gravity tool balancers to address this problem. Not only does this expand Dewalt’s product offerings through a whole new line of accessories, it helps to prevent injuries due to fatigue and overuse.
Tool balancers change the game for women in the workforce. These tool balancers would be available to pair with an array of Dewalt products. Heavy and bulky nailers and staplers would become accessible to a whole new demographic. This insight makes an impact on equality across the workforce, broadening markets, opening jobs to more individuals, and challenging changing stereotypes. Using design to make deep and lasting social impact is what drives me to work as a design strategist.